The Campfield Musical Instrument Works
The Salvation Army produced instruments normally found in a British-type brass bands. Besides the main models "OUR OWN MAKE", "TRIUMPH", "TRIUMPHONIC" and "BANDMASTER", there were other models made for youth bands or special reasons that existed for short periods.
"The Bandmaster" was one of the main models produced of the factory.
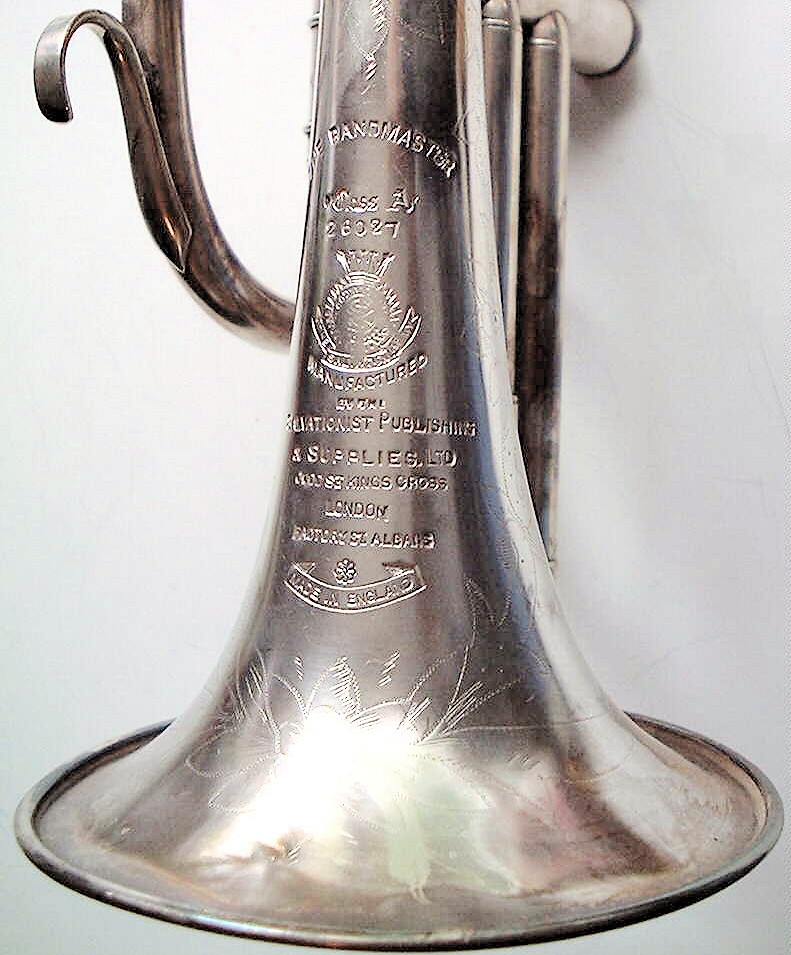
Years ago The Salvation Army had its own factory in London for making brass instruments. To receive some information about this factory, the Salvation Army Museum, Basel, conducted an interview with William Scarlett. But who is he?
William Scarlett, of Chicago, USA, has spent a lifetime around brass instruments. Born into a Salvation Army family with roots in the UK, he started learning the cornet at an early age, went to a university to study music (trumpet), worked for a Chicago trumpet maker and eventually joined the Chicago Symphony Orchestra trumpet section for 33 years. His hobbies for many years have included restoring antique instruments, researching early instrument makers and collecting examples of their instruments. In the USA he has produced a number of exhibitions of instruments made by early US makers and is considered an authority on their histories. In recent years his research has been centered on the history of The Salvation Army instrument factory at St. Albans, UK.
Bill, can you tell something about the development of The Salvation Army instrument factory and where this factory was located?
In May of 1889 The Salvation Army opened a brass instrument repair shop at IHQ with 2 experienced brass instrument workers and one 16 year old boy. Within a few years the shop began to make some instruments with parts bought from other makers. In 1893 the shop made its first complete cornet and called the models, "OUR OWN MAKE", followed by "TRIUMPH" models in 1896.
By 1896 the shop could make all of the brass band instruments. General William Booth required that all Salvation Army bands buy their instruments from this growing factory. The number of workers increased plus the factory location was moved several times in the 1890s for more space to make instruments. The Salvation Army established a real factory in 1901 in the city of St. Albans, north of London, which was used until the factory closed.
What was the name of the factory?
The Campfield Musical Instrument Works. But no instrument has been found with this name on it.
Was the factory involved in a social program for homeless or out-of-work people?
It is possible that some of these were employed but making instruments requires years of training and experience to be a valuable worker.
What kind of instruments were produced in the Salvation Army factory?
The factory only produced the instruments normally found in a British-type brass band although in the early years it also made pocket Bb cornets and a patented Eb bass trombone. Besides the main models "OUR OWN MAKE", "TRIUMPH", "TRIUMPHONIC" and "BANDMASTER", there were other models made for youth bands or special reasons that existed for short periods.
You worked for a Chicago trumpet maker and you restore also instruments. How are brass instruments made? Do you need machines to produce brass instruments or is it all made by hand?
Books have been written about this subject. In short, makers buy brass in sheets, rods and tubes and change them many times. Each time a piece of metal is changed by cutting, bending, softening, soldering, threading or any other modification, it is called an "operation". There are over 1200 operations needed to make just one cornet. Many of these operations are done on machines but much handwork is necessary even on the most mass-produced instruments of today.
Bill, do you know if there was anything special about the Salvation Army instruments?
William Booth wanted The Salvation Army to produce whatever The Salvation Army used in its’ work. When he started to use brass bands, their mission was to attract crowds on the street corners and to assist in the services. Sometimes these corners were hostile and band members and their instrument were treated roughly. Salvation Army instruments were made with thicker metal to better withstand this abuse and heavier silver plating was applied on the surface to last longer.
Were the instruments of this factory sold only to members of The Salvation Army? What is known about the quality?
By all accounts that I have found, the factory was always behind in filling orders for the Salvation Army bands which were all over the world. Therefore, it is not likely that they sold instruments outside of The Salvation Army. However, a former factory worker told me that after WWII, they made a number of basses for the British Royal Air Force.
In the early 20th century there were many endorsements in print by various Salvation Army players. They would say how easy the instruments were to play, how good they were, etc. Today in talking to older players who played the Salvation Army instruments in former years, there seems to be a common comment that the tuning could have been better. In fairness, there were many old instruments by various makers whose tuning could have been better too.
You found out, that the factory produced only 34000 instruments in 83 years. What happened to the factory?
After WWII the commercial makers of brass instruments modernized their factories and equipment. The Salvation Army did not choose to follow. The commercial makers could make instruments better and cheaper and The Salvation Army slowly slipped behind the market. In the 1960’s the factory began losing money because of this situation. I can think of several reasons why the decision was made to close the factory.
1. The original need for the rapidly expanding Salvation Army band market had ended.
2. The Salvation Army had no research department to improve the instruments as the competition was doing.
3. The Salvation Army chose not to spend the large amounts of money to modernize.
4. Competitors often had management that worked hard to improve their products to be successful. The Salvation Army had one officer in charge from the HQ who visited the factory once a week while the workers continued to make instruments the same way that they had been made for decades.
5. The competition was making better instruments for less. The Salvation Army bands could easily buy good instruments from other makers.
The factory in St. Albans closed in 1972 although by agreement, Boosey and Hawkes continued to make the "Bandmaster" cornet and "Triumphonic" tenorhorn for The Salvation Army until 1979. We will always appreciate the men and women connected with this colorful part of Salvation Army history and the contribution they made to the history of Salvation Army bands.
Thank you very much for your answers.
The stamp on this cornet shows, that it was made more than 100 years ago, while the factory was located on the Fortess Road (London, UK)

In the past The Swiss Salvation Army sold various instruments with the crest of The Salvation Army on it but had no brass factory. They were handled by the Trade Department which is stamped on the bells in French and German.
